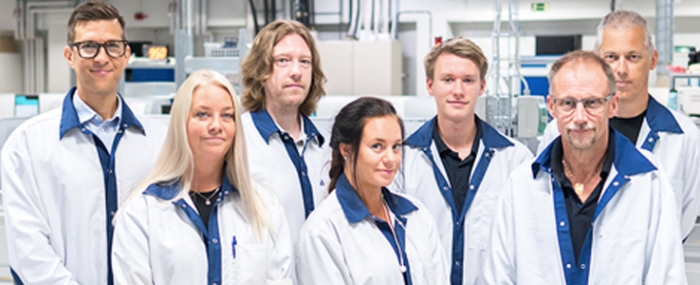
© Inission
Elektronikproduktion |
Inission: ”Flödesorienterad produktion är här för att stanna”
Kontraktstillverkaren har genomfört ett projekt vid fabriken i Munkfors för att förbättra kvalitet, ledtid och arbetsmiljö.
Inission har sedan flera år tillbaka ett arbetssätt kallat Inspirit. Det är bland annat baserat på LEAN och fokuserar på kundvärde och skapandet av effektiva processer.
Enligt ett pressmeddelande har en projektgrupp använt dessa principer i ett projekt vid fabriken i Munkfors för att förbättra kvalitet, ledtid och arbetsmiljö.
– I svensk industri finns en tradition att organisera arbetet i olika processteg, där hela arbetet görs i stora partistorlekar innan det skickas vidare till nästa processteg. Det leder till långa väntetider, sämre kvalitet och mycket slöseri. Vi vill förändra detta och arbetar aktivt med att organisera arbetet i kontinuerliga flöden med små partistorlekar, helst i enstycksflöde, säger Thomas Åström, Chief Lean Officer på Inission projektledare i det aktuella fallet, i pressmeddelandet.
Kontraktstillverkaren skriver att varje enstycksflöde är unikt och skräddarsys utifrån de förutsättningar som finns baserat på produkten som ska tillverkas. Projektet i Munkfors inleddes med att projektgruppen gemensamt gjorde en värdeflödeskartläggning och nulägesanalys för att hitta potential för förbättringar. Utifrån detta säger man sig ha identifierat en mängd förbättringsmöjligheter inom inköp, produktionsplanering, arbetsmiljö och montering.
Därefter sattes målsättningar att bland annat halvera ledtiden och förbättra både kvalitet och produktivitet.
– Till en början fanns en farhåga inom produktionsteamet att det nya arbetssättet skulle kännas stressigt och leda till försämrad arbetsmiljö. När vi berättade om projektmålen kom kommentarer som ”detta är fantasitider”. Med facit i hand instämmer nog alla i att arbetsmiljön istället förbättrats. Det är roligare att jobba och det har infunnit sig en slags lagkänsla eftersom vi numer är beroende av varandra. Det är också lättare att planera jobb då ledtiden varierar mindre. Målen vi satte upp har vi dessutom nått med marginal, säger Henrik Jansson, Team leader Inission Munkfors, i pressmeddelandet.
När enstycksflödet var i sin vagga fanns det enligt bolaget många förbättringsförslag.
– En huvuduppgift var att skapa ett balanserat och taktat enstycksflöde. Tanken var att det skulle ta lika lång tid på varje station så att flödet inte stoppades upp. Tidigare var det ett problem med variation i monteringstiderna, vilket försvårade för flödesmontering. Genom automatisering av vissa arbetsmoment och ett överenskommet standardiserat arbetssätt minskade variationen kraftigt. Vi kunde då omfördela och koppla ihop arbetsmomenten till en sammanhängande sekvens av arbetsmoment för slutmonteringen till det att produkten låg packad och klar för leverans. Det märks att det har varit ett stort engagemang runt projektet. Alla har bidragit och tillsammans har vi skapat lösningar som sparat oss mycket tid. Det har varit en inspirerande resa och nu ser jag fram emot att utveckla fler flöden, säger Ola Lindén, Produktionstekniker Inission Munkfors, i pressmeddelandet.
I nuläget finns ett flertal olika produktionsflöden på Inission Munkfors, och det säga planeras för fler. Bland fördelarna listar bolaget bland annat lättare att planera jobb, bättre kvalitet och betydligt kortare ledtid.
– Det känns jätteroligt. Det är ett kvitto på att vi tänkt rätt gällande flödesorienterad produktion och att principerna i Inspirit fungerar. Tack vare ett stort engagemang, påhittighet och tillämpning av våra principer har vi lyckats förbättra för både kund och medarbetare, fortsätter Thomas Åström i pressmeddelandet.